TİTREŞİM ANALİZİ ile KESTİRİMCİ BAKIM
Üretimi etkileyen en önemli faktörlerden biri de bakımdır. Bakım hem maliyetiyle hem de sebep olduğu zaman kaybıyla bütün bir üretim hattının durmasına sebep olabilir. Bu yüzden cihaz bakımları iyi planlanmış ve kontrollü bir şekilde gerçekleştirilmelidir.
Makinelerde üç farklı bakım tekniği uygulanmaktadır. Bu farklı tekniklerden seçim yaparken maliyet, süre, ihtiyaç, aciliyet vb. kriterler devreye girmektedir.
DTA Mühendislik bünyesinde sağladığımız titreşim analizi ile kestirimci bakım tekniğinde dönen makinelerde oluşabilecek yaygın hataları bulup, analizini gerçekleştirmekteyiz. Bunlardan bazıları; eksen kaçıklığı, yatak problemleri, balanssızlık, eğik parçalar, ayarsız ve eksantrik montajlar gösterilebilir. Bu tip hataları bulmak için kestirimci bakım alanında dünyada ilk sırada yer alan COMMTEST firmasının çözümlerini kullanmaktayız.
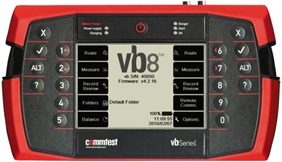
1. BOZULUNCA BAKIM – BREAKDOWN MAINTENANCE
Bu tip bakım işleminde makine bozuluncaya kadar herhangi bir müdahale gerçekleştirilmez. Makine, keyfi olarak istenilen kapasitede ve sürede çalıştırılır, herhangi bir parça bozulup makine durana kadar üretim devam eder. Bu bakım tekniği, değiştirilmesi gereken parçanın bulunabilirliği yüksek ve maliyeti düşükse avantajlıdır. Üretim kaybı çok fazla olacak ve beklenmedik zamanlarda beklenmedik maliyetler ile karşı karşıya kalma durumu söz konusu olacaktır. Dezavantajları, olumlu yönlerine göre çok daha fazla olduğundan günümüzde birçok işletme bu bakım tekniğinden vazgeçmiştir.
2. KORUYUCU BAKIM – PREDICTIVE MAINTENANCE
Koruyucu bakım tekniğinde, düzenli periyotlarda bakım işlemi gerçekleştirilir. Böylece makinenin tüm aksamlarındaki problemler düzenli aralıklarla yapılan bakımlarda tespit edilmeye çalışılır. Arızanın meydana gelmesi beklenmez, periyodik bakımlar yapılarak potansiyel arızaların oluşmaması sağlanmaya çalışılır.
Bozulunca bakım yöntemine göre daha avantajlı olduğu düşünülse de bakım periyotlarının sıklığının ayarlanması, yüksek maliyeti ve tecrübe esaslı olması gibi dezavantajları bulunmaktadır.
3. KESTİRİMCİ BAKIM – PREDICTIVE MAINTENANCE
Önceki iki tekniğe göre daha avantajlı olan kestirimci bakım tekniğinde, makine bozulduğunda veya periyodik olarak değil, gerektiğinde bakım işlemi gerçekleştirilir. Makinenin bakıma ihtiyaç duyduğunu belirtebilecek bir parametre belirlenir ve bu parametredeki değişimlere göre gerekli bakım gerçekleştirilir. Makinelerde bu parametre genelde titreşim, sıcaklık, ses veya yağ partikülleridir.
Kestirimci bakım için seçilen parametre belli periyotlarda seviye ölçümleri yapılarak izlenir. Makinenin iyi kondisyondaki ölçüm seviyeleri veya yeni bakımdan çıkmış haldeki ölçüm seviyeleri referans alınarak, belirli zamanlarda tekrar ölçümler gerçekleştirilir. Referans değerinden başlayarak devam eden bu periyodik ölçümlerde seviye değişimleri makinenin durumu hakkında önemli bilgiler vermektedir. ISO, TSE veya benzer standartlar ile karşılaştırılarak makinenin bakıma ihtiyaç duyup duymadığı önceden belirlenebilir. Tehlikeli seviyelere ulaşılan makine bakıma alınarak gerektiğinde planlı olarak üretimi durdurmak amaçlanır. Bu sayede planlı bir bakım uygulanarak makineden elde edilecek verim maksimum seviyeye çıkarılır. Kestirimci bakıma geçen işletmelerde bakım giderleri bu teknik sayesinde %50 ile %80 arasında azalmıştır.
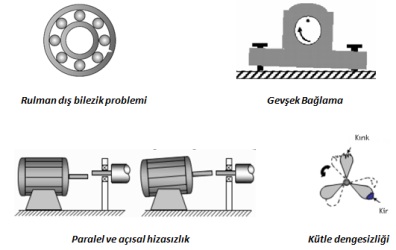
1.1. Termografi (Sıcaklık Analizi)
Kullanım alanları sıcak bölgelerin fazla olduğu işletmelerdir. Sıcaklık ölçüm cihazları ile sıcaklık seviyesindeki değişimler ölçülür. Sistemin arızalanarak işleyişin aksamasına sebep olacak sıcaklık seviyesi belirlenir ve bu seviyeye yaklaşıldığında müdahale gerçekleştirilir.
1.2. Yağ Analizi
Makinelerde birbirine temas ederek hareket eden parçalarda yağlama ve film tabakasının oluşumu önem arz eder. Temas yüzeylerindeki yağın analizi ile kestirimci bakım işlemleri için yapılan eğilim grafiği (trend plot) bilgilerine sahiptir. Kullanılan yağın fiziksel ve kimyasal özellikleri analiz edilerek oluşabilecek arızalar ile ilgili yorum yapılıp müdahale edilebilir.
1.3. Titreşim Analizi
Son 20-30 senedir yaygın olan bu yöntem ile dönen makinelerdeki titreşim seviyeleri periyodik ölçümler alınarak analiz edilir. Alınan ölçümlerin eğilim grafiği oluşturularak tehlikeli seviyelere ulaşan durumlarda sisteme müdahale edilir.
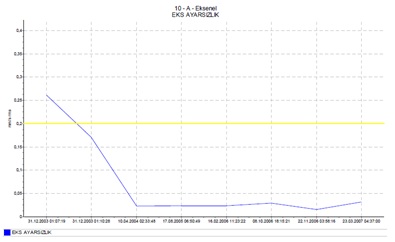
Titreşim seviyeleri incelenirken hangi titreşimin arızaya yol açabileceği ve hangi hatadan kaynaklandığının bilinmesi önemlidir. Ölçüm alındığında ortaya çıkan grafikte incelenmesi gereken iki önemli parametre bulunmaktadır; frekans ve genlik. Makinenin dönüş hızından yola çıkılarak belli frekanslarda yüksek şiddetteki titreşimler tehlikeli durumlara işaret edebilir. Sistemde oluşan her tipik hata farklı bir frekansta ortaya çıkmaktadır. Ölçüm ardından yapılan titreşim analizinde ise hangi frekansta hangi hatanın meydana geldiği tespit edilmektedir.